Greening the industry: Azerbaijani pellets producer “Green Blue” LLC benefits from taking part in the EU4Environment company assessment
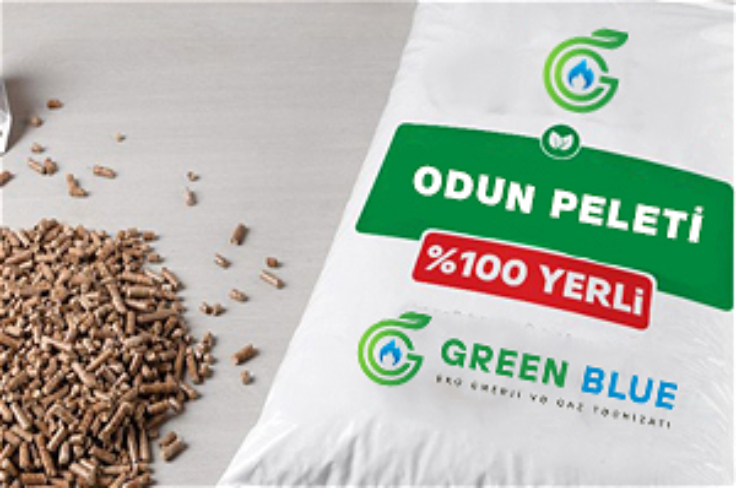
The exponential threats of climate change, paired with the need to reduce greenhouse gas emissions have led to an increased demand and use of biomass as a source of energy. In some areas in the world where the heating demand is high (such as in countries and regions with harsh and long winter seasons), woody biomass in the form of stem wood, wood chips, or wood pellets has become a typical means to produce heat.[1]
Wood pellets in particular have become extremely popular in the last 15 years. Today, they are commonly used as energy source as they are regarded as a renewable, environmentally-friendly, and sustainable option. This goes in line with recent demand trends, as the global market size for wood pellets was estimated at USD 8.23 billion (6.96 billion EUR) in 2021, with a predicted annual growth rate of 5.5% from 2022 to 2030.[2]
The production process
Wood pellets are an eco-friendly and solid fuel made from compacted sawdust and related industrial wastes resulted from the milling of lumber.[3] The production process involves grinding wood into small particles which are afterwards dried and compressed into small cylindrical pellets. The quality control in the pellets production then ensures that the dust is kept at a low level, resulting in a fuel with a consistent performance. Figure 1 (below) describes the production process in more detail.
Figure 1. Wood pellets production process.
The pellets are stored in halls and silos so that a year-round supply of fuel can be secured for all consumers. The wood pellets must also be stored indoors, in dry conditions, as they rapidly absorb moisture. After the production process is complete, the pellets are stored at the production facilities before being transported to customers for storage and use. Large-scale users, such as municipal heating companies and housing co-operatives, usually store their pellets in large silos. Small-scale users store their pellets in domestic storage rooms or sheds.[4]
The advantages of using wood pellets as fuel
Wood pellets present several advantages over conventional fossil fuels, such as:
- Cost-effectiveness: Wood pellets present economic advantages, being around 50% cheaper than conventional fuels (compared to oil or natural gas); they also are a highly efficient means of heating, converting over 90% of fuel energy into usable heat.
- Comfort: wood pellets that are used in central heating systems provide a high user comfort, easy operation and management, and are clean. In addition, the automated processes (such as fuel delivery, ignition, control, cleaning, and ash removal), are all aspects that make this heating option all the more convenient.
- Eco-friendliness: wood pellets are an eco-friendly source of energy as the wood absorbs the same amount of CO2 during growth as emitted during combustion (if sourced from sustainable forests). These pellets also achieve a reduction of CO2 emissions of over 95%, compared to furnace oil. The pellets emit low levels of emissions as they are a dry type of fuel with an efficient combustion (generating the minimum level gas emissions in combustion).
“Green Blue” LLC and its path towards a Resource Efficient and Cleaner Production (RECP)
“Green Blue” LLC is a producer of wood pellets from Azerbaijan. The company is situated in the western part in Mingachevir, the country's fourth largest city. “Green Blue” LLC operates as a small pellet production enterprise, producing pellets with diameters of 8 and 9 mm, based on a line capacity of 1500 kg/hour.
The main process represents the conversion of wood waste into fuel pellets. The company originally focused only on the wood waste generated from timber processing. In time, and as it became part of an innovative project in collaboration with the Mingachevir City Executive Power Housing and Communal Services Production Association, the company started processing trimmings, trees, shrubs, as well as their remnants. The result products are now conscientiously sold to both local and international markets in various forms (for instance, the fuel pellets are used in small boilers for efficient household heating).
One of the company’s priority areas is to ensure the high quality of its products. Hence, controlling the moisture of the raw materials is essential for an effective manufacturing process, as the pellets' popularity stems from their low moisture content (below 10%), which guarantees high efficiency and minimal smoke during combustion. Maintaining the right moisture level is crucial; an excessive moisture (of 11-12%) leads to the pellets crumbling, rendering them unsuitable for heating, while very low humidity (below 5%) has a similar effect. Therefore, the pellet production process skips the drying of raw materials, as the timber waste is already dry and currently, the company cannot control the moisture levels of the pellets.
The pellet production process also involves potential fire or explosion hazards, requiring robust prevention and protection measures, as a risk of spontaneous combustion can arise during the extended storage periods of the raw materials. Dust generation is another challenge during pellet production. Here, a dust collection system could enhance environmental conditions, promote material recycling, and reduce fire risk.
The company recently completed the RECP Demonstration Project under the EU4Environment Action, in which it received various RECP recommendations. Nowadays, the company's overarching objective is to improve resource efficiency as well as the well-being of its employees, followed by an interest in reducing the negative impact on the environment.
During the RECP assessment, the RECP experts have identified several options and highlighted three that could further support the company achieve its goals. The measures consist of:
- implementing a low-temperature belt dryer as a viable choice for maintaining consistent moisture levels for the raw material (a critical factor given the company's inability to accept high-moisture raw materials without a dryer)
- installing a fire warning and extinguishing system that can prevent fires and protect employees in high-risk areas during the production process. This system works by detecting sparks and extinguishing potential fire sources before they escalate into fires or dust explosions
- implementing a dust collection system to eliminate the dust generated in the processing of dry materials.
The total investment for all three suggested measures amounts to 70,000 EUR while the potential annual savings from introducing only the first RECP option would be of 200,000 EUR.